There is much more to know about electrodes apart from the material used to make them or whether they are consumable or non-consumable.
Before I write about the different types of rods, you need to know the general meaning of these numbers so that you can have a smooth sail in understanding them.
Check Our Recommended Welding Rods
Title | Rating | ||
---|---|---|---|
TOP | Forney 31610 E6010 Welding Rod, 1/8-Inch, 10-Pound | ![]() ![]() ![]() ![]() ![]() |
Buy Now |
Forney 30301 E6013 Welding Rod, 3/32-Inch, 1-Pound | ![]() ![]() ![]() ![]() ![]() |
Buy Now | |
Blue Demon 7014 X 5/32″ X 14″ X 5LB Plastic Iron Powder Carbon Steel Electrode | ![]() ![]() ![]() ![]() ![]() |
Buy Now | |
Forney 30681 E7018 AC Welding Rod, 3/32-Inch, 5-Pound | ![]() ![]() ![]() ![]() ![]() |
Buy Now | |
Blue Demon 7024 X 1/8″ X 14″ X 5LB Plastic High Speed Carbon Steel Electrode | ![]() ![]() ![]() ![]() ![]() |
Buy Now |
The first two numbers on the size number of the electrode usually represent the tensile strength of the electrode. 70, for example, implies that the electrode has a tensile strength of 70,000 pounds per square inch.
The third digit represents the position in which you can use the rod.
The number 1 stands for all position, 2 for flat and horizontal position, and 4 stands for overhead, vertical, horizontal, and flat electrode positions.
Digits on the last number denote the coating that has been used and consequently the current that you can safely use.
Welding rod is the generic term that is used to refer to the filler metal or electrodes, which are used to join 2 other base metals when a welder is carrying out shielded metal arc welding, abbreviated as SMAW
Different numbers that appear on electrodes
The following is a table detailing the different numbers that appear on electrodes and what they mean as offered by the American Welding Society:
Digit | Coating Used | Current Used In Welding |
0 | High cellulose sodium | DC+ |
1 | High cellulose potassium | AC, DC+, DC- |
2 | High Titania sodium, | AC, DC- |
3 | High Titania potassium | AC, DC+ |
4 | Iron powder, Titania | AC, DC+, DC- |
5 | Low hydrogen sodium | DC+ |
6 | Low hydrogen potassium | AC, DC+ |
7 | High iron oxide, potassium powder | AC, DC+, DC- |
8 | Low hydrogen potassium, iron powder | AC, DC+, DC- |
Different sizes of stick electrodes
There are many sizes of stick electrodes. They come in different diameters with varying recommended amps as shown in the table below:
Diameter of electrode in inches | Electrodes | Thickness of Metal | |||||
6010 and 6011 | 6012 | 6013 | 7014 | 7018 | 7024 | ||
1/16 | 20-40 | 20-40 | Up to 3/16” | ||||
5/64 | 25-60 | 25-60 | |||||
3/32 | 40-80 | 35-85 | 45-90 | 80-125 | 70-100 | 100-145 | Up to ¼” |
1/8 | 75-125 | 80-140 | 80-130 | 110-160 | 115-165 | 140-190 | Over 1/8” |
5/32 | 110-170 | 110-190 | 105-180 | 150-210 | 150-220 | 180-250 | Over ¼” |
3/16 | 140-215 | 140-240 | 150-230 | 200-275 | 200-275 | 230-305 | Over 3/8” |
7/32 | 170-250 | 200-320 | 310-300 | 260-340 | 260-340 | 275-365 | |
¼ | 210-320 | 250-400 | 250-350 | 330-415 | 315-400 | 335-430 | Over 3/8” |
5/16 | 275-425 | 300-500 | 320-430 | 390-500 | 375-470 | 400-525 | Over ½” |
As seen from the table above, you can tell what diameter of a welding rod you can use and the metal thickness you can use it on, for best results.
Different Welding Rod Sizes & Classification
Note that the thicker the material to be welded is, the higher the current needed, and the larger the electrode needed. The common electrodes include: 6010, 6011, 6012, 6013, 7014, 7018, and 7024
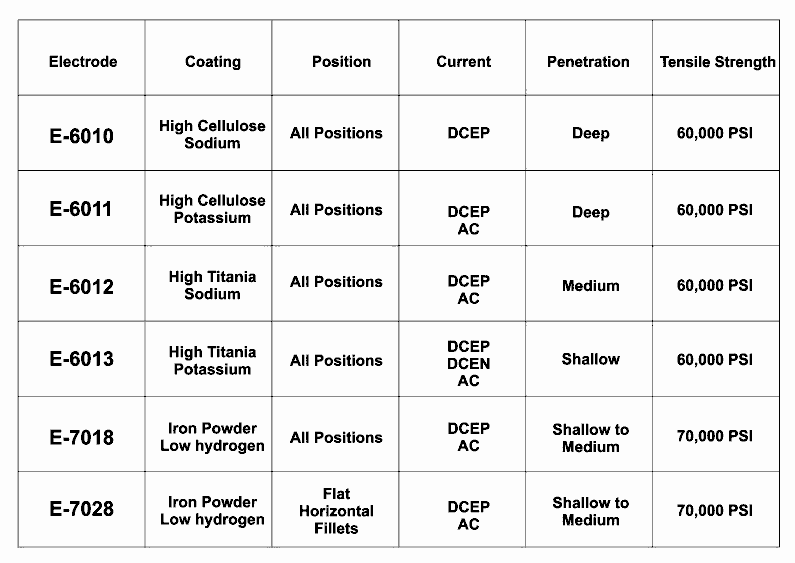
Let us look at these sizes below:
6010 Electrodes
These are only usable with DC power as they come with a high cellulose sodium coating, have deep penetration, and can also pass through dusty, rusty, and oily metals including those with paint.
As you can tell from the third digit 1, it is an all position electrode and can be used for pipe welding as it runs smoothly, and its slag is easier to remove.
They are suitable for experienced welders as the novice ones would find them harder to use based on the fact that they have a tight arc.
The 6010 electrode has many applications, and it is common among welders though it is not necessarily easy to use.
It can survive at room temperature under dry conditions. You should dry up any moisture before use, and it is worthy to note that drenching of electrodes destroys them.
Forney 31610 E6010 Welding Rod, 1/8-Inch, 10-Pound
- All position welding rod with digging arc, deep penetration on dirty, rusty and painted materials
- Ideal for joints requiring deep penetration such as square edge butt welds, good for vertical and overhead welding with light slag
- Minimal surface preparation required
- Excellent for galvanized steel and rusty/oily steel in maintenance or repair applications, plus pipe welding
- Click on the (BY FORNEY) name above in blue under the title to view our full catalog of Welders, Abrasives, Chain/Wire Rope, Tools and more!
6011 Electrodes
These have a high cellulose potassium coating hence can use an Alternating Current (AC) as well as a DC+ current.
Just like the 6010, they are position electrodes and can also cut deep through rusty, unclean materials, making them popular among welders mostly for maintenance works whenever a direct current (DC) power is not available.
You can use them with any welding material.
The slag produced by these electrodes is small but is more difficult to remove compared to other electrodes.
Forney 31205 E6011 Welding Rod, 1/8-Inch, 5-Pound
- The product is 5LB 1/8 6011 Weld Rod
- Easy to use
- All position welding, all purpose rod for deep penetration and fast freezing on dirty, rusty and painted materials
- Smooth arc wetting and spread with good spatter providing fast deposition and flatter contour fillets offering faster travel speeds
- Minimal surface preparation required
6012 Electrodes
These are also all position electrodes that work well in gap-bridging applications between joints. They are also used for high speed and high current fillet welds done horizontally.
Unlike the 6010 and 6011 electrodes, their penetration is shallow, not to mention the slag produced after welding that will require a lot of cleaning.
6013 Electrodes
The 6013 wed rods can withstand 60,000 pounds of stress per square inch. These rods are compatible with AC, DC+, and DC- currents.
The ability to handle these different currents makes it very versatile and usable with any welding machine including small machines, unlike other welding rods which require larger machines.
Other features of the 6013 electrodes are that they are suited for lighter jobs such as automotive projects, they have a moderate and not much slag which can easily be removed.
Contrary to the 6012 sizes, and they produce soft arcs with fewer spatters and can only be used for welding material that is clean, new, and free of rust, automotive projects.
The 6013 has medium penetration on thinner sheet metals.
When welding with 6013 electrodes, move them in small circular motions around the joint. This produces stronger welds and helps to control speed. The 6013 is also an enemy of water and any moist conditions. Store 6013 electrodes in a moist free and moist proof container.
Forney 30301 E6013 Welding Rod, 3/32-Inch, 1-Pound
- The product is LB 3/32 6013 Weld Rod
- Easy to use
- All position welding, general purpose rod for shallow penetration or in poor fit up conditions
- Excellent wetting action, yielding smooth and flat beads with steady arc with either AC or DC
- Low spatter and excellent slag removal, virtually self cleaning in vertical down fillets
7014 Electrodes
These electrodes have the same joint penetration as the 6012 and are suitable for use on carbon and low-alloy steel. They have a high amount of iron powder, hence increasing the depositing rate.
They can withstand higher amperages compared to 6012 electrodes. These are used for construction equipment, farm machinery, barges, metal fixtures, and automotive parts.
Blue Demon 7014 X 5/32″ X 14″ X 5LB Plastic Iron Powder Carbon Steel Electrode
- E7014 offers outstanding slag removal and bead appearance
- This rod is ideal for jobs that require high deposition and speed of travel
- Typical applications include ornamental iron, machine bases, heavy sheet metal and frames
7018 Electrodes
They are the easiest to use among the electrodes and come with a thick flux, and their powder content is high. They have minimal penetration, producing a smooth and quiet arc with fewer spatters.
Of course, they are all position rods which can bear 70,000 pounds of stress per sq. Inch. They have an iron powder low hydrogen coating meaning they can be used with both AC and DC+ currents.
Their low hydrogen content is what translates to smooth welds which are also strong. The secret to achieving these smooth and strong welds is to drag the rod across the surface of the metal as you also move it slightly from side to side.
Low hydrogen rods, however, come with their cons, for example, the need for special storage to ensure they serve you for a longer period of time.
They have zero tolerance for water or any form of moisture. You can store them in an oven at 250 degrees F. If you can buy your own, the better. 7018 electrodes are popular because 7018 electrodes are popular as they can weld thick materials like steel, and they produce strong welds.
They are ideal for structural welding, nuclear power plants, pressure pipes, and large bridges. They are also known as ‘drag rods’ or ‘high-low’ rods.
Forney 30681 E7018 AC Welding Rod, 3/32-Inch, 5-Pound
- The product is 5LB 3/327018AC Weld Rod
- Easy to use
- All position welding, low hydrogen rod for general purpose AC applications requiring low penetration, can also be used on DC+
- Excellent bead contour, light spatter and slag is often self cleaning
- Good performance with low open circuit-Voltage OCV power sources
7024 Electrodes
Their powder content is also high increasing the rate of deposition. These are used in flat and horizontal positions as they have a big and hot puddle with the flux causing the metal to slowly solidify.
7024 electrodes do well in a quarter inch thick or more steel plate and are also suitable for metals more than a half inches thick.
These electrodes do not require a rod oven, they lay down a lot of weld metal, and make smooth welds and produce slag that is easy to clean.
Additionally, they are not pricey. They, however, require one to use a lot of heat which poses a threat to the welder.
Blue Demon 7024 X 1/8″ X 14″ X 5LB Plastic High Speed Carbon Steel Electrode
- Excellent bead appearance and self-cleaning slag give it operator appeal
- This electrode has good weldability and superior mechanical properties
- Typical applications include ship building, bridges, structural steels, machine bases, truck fabrication, storage tanks
What factors do you consider when choosing a welding rod size?
Okay, the welding rod you choose should be able to meet your welding needs. The factors that should be taken into consideration include:
- Tensile Strength
The minimum tensile strength of the electrode should match that of the base metal. As you already know by now, you will determine the tensile strength of an electrode by checking out its first two digits which are usually printed on its side.
For example, if the first two digits are 60, say for a 6011 electrode, it has a tensile strength of 60 psi and would function best with a metal of matching tensile strength. This match of strengths will prevent cracking when welding and other inconveniences.
- Current in Use
Determine if the electrode you are about to use can be connected with either an AC or DC power source or both.
From the table above, you see that some electrodes are compatible with either of the two and can, therefore, be used with whichever power source you have in place. Current used also has an effect on the level of penetration.
- Weld Position
Consider the weld position by looking at the third digit in the classification. For example, an electrode with a digit 1 as the third number can weld in any position, either flat, vertical, overhead, or horizontal, while that with a digit 2 can only be used for flat and horizontal positions.
- Base Metal
The base metal thickness, joint fit-up, and shape should also be put into consideration. Thick materials work well with a highly ductile and low hydrogen electrode as this prevents the electrode from cracking.
Electrodes that can be used with thick materials include those that end in digits 15, 16, or 18.
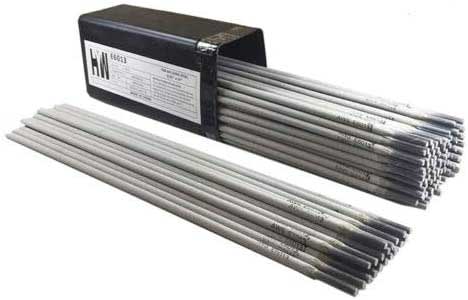
Thinner materials need an electrode such as the 6013 that produces soft arcs and those that produce shallow penetration to prevent burning of the materials.
If a joint design or fit-up is not beveled, then an electrode such as 6010 or 6011 that has deep penetration is a good choice. For wide openings, an electrode such as 6012 will help bridge gaps and make groove welds.
- Polarity
Polarity is the direction in which the current flows in a circuit. In the case of straight polarity, the electrode is negative and the workpiece positive. Hence the electrons flow toward the workpiece.
For reverse polarity, the electrodes flow toward the electrode because the workpiece is negative and the electrode is positive.
With electrodes that can accommodate AC, the polarity is not an issue, but with those that use DC current, one can weld either by using reverse or straight polarity.
- Need To Cut Through Environmental Contaminants
The kind of electrode you use also depends on the outward condition of your metal. Is it new and clean, or rusty and corroded?
For a new and clean metal, use electrodes such as the 6013 electrodes, and for unclean metals, use the 6010 and 6011 electrodes.
- Specifications of Use
The conditions in which your welding will be kept will determine the electrode you use. If it will be kept or used in conditions of high heat or low heat, use of a hydrogen electrode reduces the prospects of cracking.
Special welding specifications requiring you to use specific types of electrodes are available for use on critical projects such as boiler fabrications.
Frequently Asked Questions
How do I choose the best amperage for welding?
All you need to do is use the amperage table for different electrodes as well as their diameters. Use an amperage that is within the range given for that particular electrode. Refer to table 2 above for details.
How do I choose the best size of electrode?
The electrode you choose depends on many factors such as the thickness of the material to be welded. A thin electrode for a thin plate and a thick electrode for a thick plate.
Wrapping Up
To be able to select the correct size of electrode you need to carry out your project, you need to be able to understand the different sizes of welding rods that are available, when, and how they can be used.
There can even be several choices for one project. By using the factors that you need to consider, you will easily be able to determine which among the different sizes of welding rods is suitable for your use. (Based on factors such as power source and welding position.)